Industrial custom molded rubber and polyurethane rollers from Mark Tool Co., Inc. have a wide variety of applications in the production of paper, steel, food, textiles, wood, and plastic.
These rollers protect, squeeze, feed, insulate, and move products, and there’s a different size required for every job. Depending on the task at hand, the right roller for the job has to have the correct bearing rating, axle deflection, and tube strength. They have to be made of appropriate materials, and their shape can vary depending on the function.
For example, our cast polyurethane rollers are made from high-quality polymers tooled precisely into one of hundreds of shapes and sizes, such as the hourglass or V-shaped rollers you see below, commonly used for conveyor belts, pipe conveyors, sheaves, and paper mills.
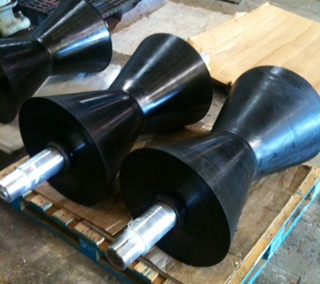
Roller Hardness
Let’s look at one of the most important characteristics of industrial rollers, perhaps the foremost quality that determines a roller’s suitability for a given task: Hardness.
Roller hardness can be defined as the roller’s resistance to indentation when a static load is applied. Industrial roller hardness is measured via two common methods:
Pusey & Jones: Also known as "P & J hardness,” this scale ranges from 0 (the hardest material) to 100 (the softest). The measurement is always taken (using an instrument known as a "plastometer”) 60 seconds after the static load is applied. The Pusey & Jones scale is common in the paper industry.
Durometer: The international standard used to measure the hardness of rubber, durometer is common in industries from printing to coating. Durometer readings can be made immediately or up to 15 seconds after load is applied.
"Durometer” also refers to the instrument used to measure hardness. Today’s durometers are based on the "Shore” scale instruments that measure soft materials (00 scale) up to extremely hard materials (D scale). Each scale range is from 0-100, and the higher the number, the harder the roller (opposite from Pusey & Jones readings).
Shores A and D are the most widely used scale for the rubber and polyurethane roller industry. Mark Tool offers cast urethane industrial rollers ranging in hardness from Shore 10A to Shore 80D.

Image courtesy of Smooth-On, Inc.
Accurate Readings
To get the most accurate hardness measurement, the following must be taken into account:
- The ambient temperature: Some materials are susceptible to temperature change. In other words, they will be softer when it’s warmer and they will be harder when it’s colder.
- Durometer/plastometer placement: The base of a hand-held durometer must be parallel with the axis of the roller journals or support shaft. The operator should apply a steady uniform force lowering the entire base so it touches roller surface in a parallel manner as the indenter penetrates the material. A plastometer must be held perpendicular to the roller surface, and the load must be applied quickly to avoid "shocking” the instrument.
- Roller thickness: If less than 0.25 inch thick, you may get a slightly higher durometer reading. Be sure to take thickness into account.
Terms to Know
The industrial roller industry has a language all its own. Aside from the terms above that describe hardness and measuring roller strength, here are a few additional key phrases and word you’ll hear.
Abrasion Resistance: Abrasion, grinding, or wearing away due to friction, will be an issue for any industrial roller--no matter its hardness. Coatings that are abrasion-resistant can reduce this friction.
Coefficient of Friction (COF): Rollers move something else along via motorized conveyor systems, right? Coefficient of friction refers to the force required to make the belt material slide over the rollers.
A lower COF means the rollers don’t require much power to keep the belt moving. Teflon has a low COF because it slides against steel easily. Most elastomer compounds have a high COF because they resist sliding against steel rollers.
Crown: A difference in diameter between the center of a roller covering and various points on the face is required to compensate for deflection. The "crown” is simply the shape of the roller, meant to achieve a uniform nip pressure distribution.
Deflection: This is the degree of bend in an industrial roller when pressure is applied.
Hydrolytic Stability: The measure of resistance to breaking down urethane compounds exhibit when exposed to moisture.
Nip: This is the contact area between two rollers. Roller crowning is a common way to reduce the nip variation caused by roller deflection.
PLI: A measure of the force applied to a roller.
Mark Tool is a leading manufacturer of custom molded rubber products, including rubber rollers, tensioner pads and other custom molded rubber products. We got our start in oilfield and marine applications but our product line has grown to meet the needs of virtually every industry from manufacturing to food goods processing. Contact us to learn more about our products or to request a quote.